Thermal Aspect of Gas Turbine Engines in Aviation
The thermal aspect of a gas turbine engine in aviation is a critical and fundamental concept that plays a significant role in the engine’s operation and performance. The thermal aspect refers to the heat energy transformation and utilization within the engine during the various stages of the combustion and propulsion process. Here are some key points related to the thermal aspect of gas turbine engines in aviation:
Combustion Process: In a gas turbine engine, air is compressed in the compressor section and then mixed with fuel in the combustion chamber. The combustion process releases a large amount of heat energy due to the rapid and controlled burning of the fuel-air mixture. This thermal energy is converted into high-temperature, high-pressure gases.
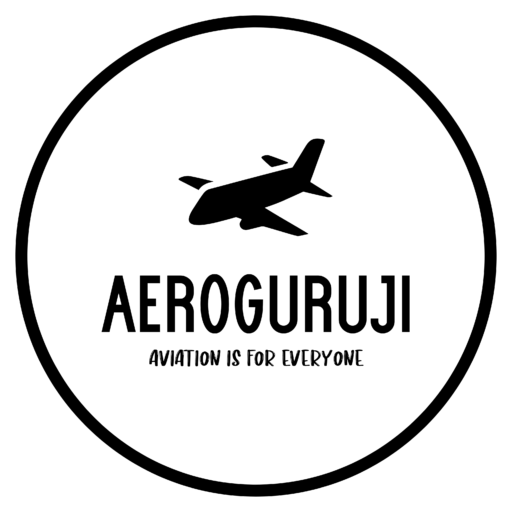
Expansion and Propulsion: The high-temperature gases expand rapidly, driving the turbine section of the engine. The expansion of gases converts the thermal energy into mechanical energy, which is used to drive the compressor and other engine components. The mechanical energy is then further converted into thrust to propel the aircraft forward.
Thermal Efficiency: The thermal efficiency of a gas turbine engine is a measure of how effectively it converts the heat energy from fuel combustion into useful mechanical work. Higher thermal efficiency means more effective energy conversion and better fuel economy, which is crucial for modern aircraft to optimize range and performance.
Turbine Cooling: During the combustion process, the turbine blades experience extremely high temperatures due to the hot gases passing over them. To prevent damage and maintain engine durability, gas turbine engines employ advanced cooling techniques to protect the turbine blades from thermal stress and creep.
Emission Control: The thermal aspect of gas turbine engines also relates to the control of exhaust gas temperature and emissions. Modern engines are designed to achieve lower exhaust gas temperatures to improve fuel efficiency and reduce NOx (nitrogen oxides) emissions, which are harmful to the environment.
Materials and Design: Thermal considerations heavily influence the selection of materials used in the construction of gas turbine engines. High-temperature-resistant materials, such as superalloys, ceramic coatings, and thermal barrier coatings, are employed to withstand the extreme conditions within the engine.
Inlet Air Cooling: In certain environments where the air temperature is high, gas turbine engines can experience performance degradation. To counteract this, some engines use inlet air cooling systems to reduce the temperature of the incoming air, improving engine efficiency and power output.
Thermal Stability: The thermal aspect is also crucial for ensuring the stable and reliable operation of gas turbine engines. Engine design and control systems aim to maintain stable operating temperatures throughout various flight conditions to prevent engine surges or stalls.
The thermal aspect of gas turbine engines is a complex and multidisciplinary field that involves engineering, thermodynamics, material science, and aerodynamics. It continues to be a focal point in aviation research and development, as engineers strive to improve engine performance, efficiency, and environmental impact.
List of Civil Aviation Authorities Worldwide- Know More