Key Uses of Composite Materials in Aircraft Designing
Composite materials have revolutionized aircraft design and manufacturing, offering numerous advantages over traditional materials like aluminum and steel. Here are some key uses of composite materials in aircraft designing:
Lightweight Structures: Composites are known for their high strength-to-weight ratio. By using composites in the construction of the aircraft’s fuselage, wings, tail, and other components, designers can achieve significant weight savings compared to conventional metal structures. This reduces fuel consumption, increases range, and enhances overall aircraft performance.
Fatigue Resistance: Composites are more resistant to fatigue than metals, which means they can withstand repeated stress cycles without degrading. This property is especially important in high-stress areas of the aircraft, such as the wings and landing gear components.
Inside Aircraft Design: The Science and Art of Building Planes
Aerodynamic Efficiency: The ability to shape composite materials more easily allows designers to create aerodynamically efficient aircraft structures. Smooth and contoured surfaces reduce drag, leading to better fuel efficiency and improved overall performance.
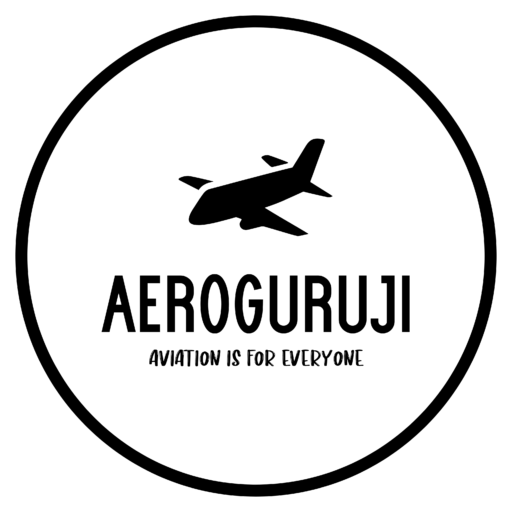
Corrosion Resistance: Unlike metal structures that are susceptible to corrosion, composite materials are inherently resistant to rust and other forms of corrosion. This property helps to extend the lifespan of the aircraft and reduces the need for frequent inspections and maintenance.
Design Flexibility: Composites can be molded into complex shapes, offering greater design flexibility to optimize the aircraft’s performance. This ability to create seamless structures with fewer joints and fasteners improves structural integrity and reduces maintenance requirements.
Noise Reduction: Composite materials dampen vibrations and reduce noise levels inside the aircraft. This contributes to a quieter and more comfortable flying experience for passengers and crew.
Thermal Stability: Composites can have excellent thermal properties, providing better insulation against extreme temperatures. This is particularly important for aircraft that operate in both high-temperature and low-temperature environments.
Repairability: Although composites can be damaged, they are often easier to repair than metal structures. Advanced repair techniques and materials allow for efficient and cost-effective repairs, reducing downtime and maintenance expenses.
Electric Conductivity: Composite materials can be engineered to have specific electrical conductivity properties. In certain aircraft designs, this can be advantageous for shielding against electromagnetic interference or lightning strikes.
Structural Integration: Composites facilitate structural integration, where multiple components can be combined into a single piece, reducing the number of parts and simplifying assembly. This streamlines manufacturing processes and enhances overall structural integrity.
Overall, the use of composite materials in aircraft design offers a multitude of benefits that contribute to improved performance, reduced maintenance, increased efficiency, and enhanced passenger comfort. As technology advances, the aviation industry is likely to continue exploring innovative ways to integrate composites into aircraft construction to meet the demands of modern aviation.